Ferro Silicon Magnesium Alloy Nodulizer
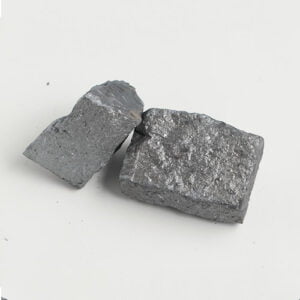
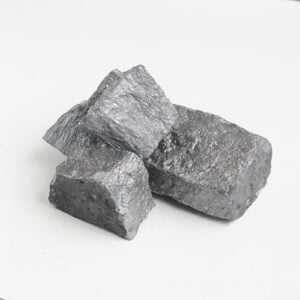
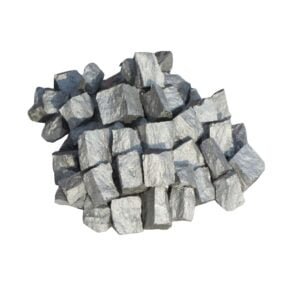
FeSiMg Alloy Nodulizer
Rare earth ferrosilicon magnesium alloy is made by adding calcium, magnesium and rare earth to ferrosilicon. It is also called magnesium alloy nodulizer. It is used in the production of ductile iron to change flake graphite into spherical graphite. It can significantly improve the strength of cast iron, and at the same time has the functions of degassing, desulfurization and deoxidation. The use in metallurgy and foundry industry is increasing. Among them, magnesium is the main spheroidizing element, which has a direct impact on the spheroidizing effect of graphite
Application and Features of FeSiMg Alloy Nodulizer
Magnesium-ferrosilicon alloy is a gray-black solid, which is formed by ferrosilicon as raw material, and the ratio of calcium, magnesium and rare earth is adjusted to the optimal range to make it react smoothly. The casting thickness of each brand of rare earth magnesium ferrosilicon alloy does not exceed 100mm; the standard particle size of rare earth magnesium ferrosilicon alloy is 5~25mm and 5~30mm. According to different purposes, customers can specify special granularity, such as: 5~15mm, 3~25mm, 8~40mm, 25~50mm, etc.
Low-magnesium nodulizers are mostly used for smelting in intermediate frequency furnaces and nodulizing treatment of low-sulfur molten iron. It has the advantages of gentle spheroidization reaction and easy full absorption of spheroidized elements.
Medium magnesium which contains 6% and 7% magnesium are mostly used in cupola furnace, electric furnace duplex smelting, or intermediate frequency furnace smelting pearlite cast ductile iron castings. According to the wall thickness of the casting and the sulfur content of the original molten iron, determine the appropriate amount of nodulizer added, which has a wide range of applications and a wide range of nodulizer treatment processes.
High-magnesium series nodulizers are suitable for cupola smelting, molten iron with a sulfur content of 0.06%-0.09%, and the addition amount is between 1.6%-2.0%. Low-aluminum nodulizers are used in castings that are prone to subcutaneous porosity defects, and castings that require aluminum content in molten iron.
Contact Us to Get Your Best Price !
FeSiMg Alloy Nodulizer Technical Specifications
Item | Chemical Elements Contents | |||||||||
% Re | % Ce/Re | % Mg | % Ca | % Si | % Mn | % Ti | % MgO | % Al | % Fe | |
ReMgSiFe-01CeA | 0.5-2.0 | ≥46 | 4.5-5.5 | 1.0-3.0 | 45.0 | 1.0 | 1.0 | 0.5 | 1.0 | The rest |
ReMgSiFe-01CeB | 0.5-2.0 | ≥46 | 5.5-6.5 | 1.0-3.0 | 45.0 | 1.0 | 1.0 | 0.6 | 1.0 | The rest |
ReMgSiFe-01CeC | 0.5-2.0 | ≥46 | 6.5-7.5 | 1.0-2.5 | 45.0 | 1.0 | 1.0 | 0.7 | 1.0 | The rest |
ReMgSiFe-01CeD | 0.5-2.0 | ≥46 | 7.5-8.5 | 1.0-2.5 | 45.0 | 1.0 | 1.0 | 0.8 | 1.0 | The rest |
ReMgSiFe-03CeA | 2.0-4.0 | ≥46 | 6.0-8.0 | 1.0-2.0 | 45.0 | 1.0 | 1.0 | 0.7 | 1.0 | The rest |
ReMgSiFe-03CeB | 2.0-4.0 | ≥46 | 6.0-8.0 | 2.0-3.5 | 45.0 | 1.0 | 1.0 | 0.7 | 1.0 | The rest |
ReMgSiFe-03CeC | 2.0-4.0 | ≥46 | 7.0-9.0 | 1.0-2.0 | 45.0 | 1.0 | 1.0 | 0.8 | 1.0 | The rest |
ReMgSiFe-03CeD | 2.0-4.0 | ≥46 | 7.0-9.0 | 2.0-3.5 | 45.0 | 1.0 | 1.0 | 0.8 | 1.0 | The rest |
ReMgSiFe-05CeA | 4.0-6.0 | ≥46 | 7.0-9.0 | 1.0-2.0 | 44.0 | 2.0 | 1.0 | 0.8 | 1.0 | The rest |
ReMgSiFe-05CeB | 4.0-6.0 | ≥46 | 7.0-9.0 | 2.0-3.0 | 44.0 | 2.0 | 1.0 | 0.8 | 1.0 | The rest |
ReMgSiFe-07CeA | 6.0-8.0 | ≥46 | 7.0-9.0 | 1.0-2.0 | 44.0 | 2.0 | 1.0 | 0.8 | 1.0 | The rest |
ReMgSiFe-07CeB | 6.0-8.0 | ≥46 | 7.0-9.0 | 2.0-3.0 | 44.0 | 2.0 | 1.0 | 0.8 | 1.0 | The rest |
ReMgSiFe-07CeC | 6.0-8.0 | ≥46 | 9.0-11.0 | 1.0-3.0 | 44.0 | 2.0 | 1.0 | 0.1 | 1.0 | The rest |
Get in Touch
Qugou Industrial Zone
Anyang City, Henan Province of China
Phone : + 86 159 37282819
Email : info@jbtmetals.com
MON-FRI 09:00 – 19:00
SAT-SUN 10:00 – 14:00

JBT produces and supplies silicon metal and ferrosilicon products, mainly products are silicon metal 553, 441, 421, 411 3303,2202, 97, silicon carbide, carbon raiser for steelmaking and casting industries. We also make electrolytic manganese metal, inoculants and nodulizers.
Get in Touch
- info@jbtmetals.com
- +86-372-5032026
- +86-15937282819
- Send Inquiry
- Online Chat
- Qugou Town, Anyang City, Henan Province of China